Para ambos proyectos, uno de los grandes retos fue producir una gran cantidad de estructuras de acero y, en el caso de OGP1, con dimensiones y peso fuera de lo común. Junto con ello, el trabajo en conjunto sustentado en la precisión.
Paula Chapple C.
Periodista BiT
OGP 1 (Organic Growth Proyect 1) de Minera Escondida y Sierra Gorda, son dos exitosos megaproyectos para la infraestructura minera en la Región de Antofagasta, que entre ambos demandaron un total de 38.000 toneladas en acero estructural.
La fabricación de estructuras en paralelo para ambas obras estuvo a cargo del Consorcio Edyce-Arrigoni y significó una producción con un alto grado de exigencia por más de 14 meses.
En el caso de OGP1, el alcance del trabajo fue el cálculo de las conexiones, modelamiento 3D, detallamiento, fabricación y aplicación del sistema de pintura para las 15.000 TM aproximadamente de estructuras que componen el Edificio de Molienda del proyecto Organic Growth Project 1 para Bechtel – BHP.
En Sierra Gorda, en tanto, el alcance del trabajo fue el cálculo de las conexiones, modelamiento 3D, detallamiento, fabricación y aplicación del sistema de pintura para las 30.000 TM aproximadamente de estructuras que componen todos los edificios principales del proyecto Sierra Gorda (Harneros, Chancadores, Molienda, Remolienda, Flotación, Filtrado, Espesadores, Planta de reactivos, Planta de aire, entre otras áreas).
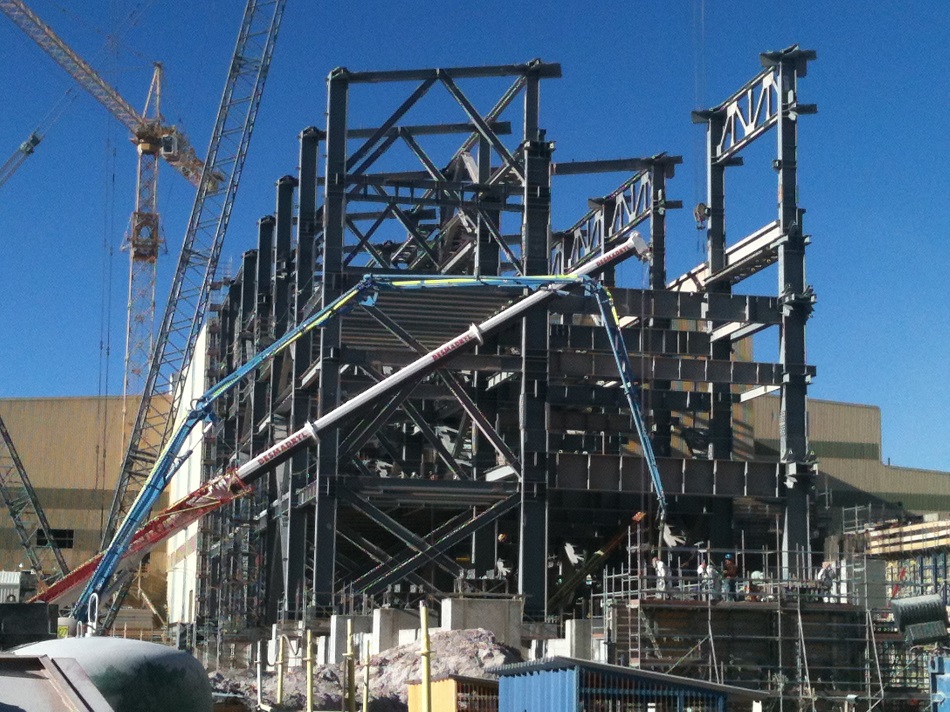
Acero en el desierto
“Uno de los grandes desafíos de ambos proyectos fue la producción de gran cantidad de estructuras de acero y, en el caso de OGP1, con dimensiones y peso fuera de lo común”, señala Mario André, gerente de Ingeniería de Arrigoni Metalúrgica.
En lo que respecta al detallamiento, uno de los primeros desafíos fue el poder asegurar la emisión de grandes volúmenes de planos a fábrica en los plazos requeridos por el proyecto. Esto sólo fue posible como resultado de la estandarización de los procesos internos y de una adecuada dotación de profesionales dedicados de forma permanente al proyecto.
Además del volumen de estructura propiamente tal, otro desafío importante fue todo lo que conlleva detallar y fabricar perfiles de gran tamaño y con planchas de 63, 75 e incluso 100 mm de espesor. Por ejemplo, “los procesos de armado de perfiles son especiales, las conexiones apernadas tienen baterías con gran cantidad de perforaciones, la manipulación de las piezas en fábrica se dificulta debido a su peso y tamaño, es decir, características que hacen que estas estructuras tengan un proceso diferente al resto de los proyectos, y para las cuales los cuidados durante el detallamiento y fabricación deben acentuarse aún más con el fin de asegurar el calce de las estructuras en terreno”, prosigue Mario André.
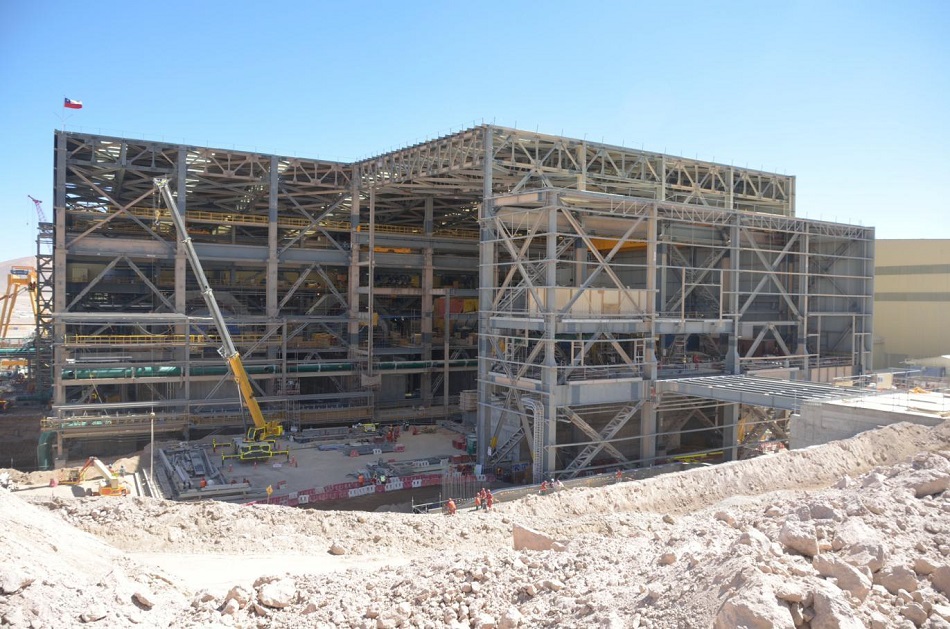
Planificación
Previo al inicio de los trabajos, se necesitaron seis meses de preparación y planificación; y del trabajo conjunto con Edyce para la ingeniería de detalle estructural para ambos proyectos.
En los primeros meses, los equipos de Ingeniería de ambas empresas trabajaron en la preparación de un “Estándar de Detallamiento de Consorcio”, en el cual fueron consolidadas las mejores prácticas aprendidas tanto en Arrigoni como en Edyce a lo largo de los años en que ambas maestranzas han estado presentes en la industria de las estructuras metálicas. “Este estándar se hizo con el objeto de optimizar los procesos y unificar criterios, de tal manera que el producto final fuese el mismo, independientemente de qué empresa realizara el trabajo”, complementa el ejecutivo de Arrigoni Metalúrgica.
En el caso de OGP1, por tratarse de un solo edificio y de gran dimensión, se tomó la decisión de trabajar con un equipo de proyectistas, instalado físicamente en un mismo lugar, el cual fue integrado por profesionales de Edyce y de Arrigoni. El objetivo de esto fue trabajar en una red local sobre un único modelo Tekla, con el objetivo de agilizar la velocidad de guardado y otros procesos y así no depender de factores externos, como por ejemplo la velocidad de banda ancha.
En el caso de OGP1, por tratarse de un solo edificio, y de gran dimensión, se tomó la decisión de trabajar con un equipo de proyectistas, instalado físicamente en un mismo lugar, el cual fue integrado por profesionales de Edyce y de Arrigoni. El objetivo de esto fue trabajar en una red local sobre un único modelo BIM (Tekla), de tal manera de agilizar la velocidad de guardado y otros procesos, y así no depender de actores externos, como por ejemplo la velocidad de banda ancha.
En cuanto a la cantidad de proyectistas destinados al detallamiento de este proyecto, se llegó a tener aproximadamente 15 personas trabajando al mismo tiempo en el modelo Tekla. Por su parte, para el cálculo de conexiones también se conformó un equipo de profesionales de ambas empresas, realizando las tareas en conjunto.
Respecto de Sierra Gorda, “como se trató de un proyecto con muchos edificios de diferentes dimensiones, éstos fueron distribuidos en función de su volumen (toneladas) y complejidad, para ser detallados y/o fabricados ya sea en Edyce o en Arrigoni. En algunos casos, edificios detallados por Edyce fueron fabricados por Arrigoni, y viceversa. Esto se pudo realizar sin inconvenientes debido a que en el detallamiento se utilizó una metodología estándar para todo el proyecto, independiente de qué maestranza realizara la fabricación”, detalla Mario André.
Logística
Durante el desarrollo de estos proyectos se despacharon desde “nuestra planta más de 300 camiones cargados con estructuras cada mes. La logística es de especial relevancia, cuando se requiere que las estructuras lleguen a terreno en el mismo orden y prioridad requerida por el contratista de montaje. Para esto nos apoyamos en los sistemas BIM y nuestros softwares de administración de producción, que nos permiten llevar el status en tiempo real de cada uno de los elementos que forman parte de los edificios y realizar las coordinaciones con la obra”, indica Mario André.
Igualmente importante fue toda la logística que se desarrolló en los patios de almacenamiento de estructuras; proyectos como estos pueden estar compuestos por más de 50.000 piezas entre columnas, vigas, diagonales, gratings, entre otras y es fundamental disponer de las estructuras de manera ordenada y según las secuencias de montaje.
Se consideró también que los proyectos se desarrollaron en zonas aisladas, con altos costos de hora hombre y hora máquina, no pudiendo perder piezas o tener gente o máquinas inmovilizadas debido a algún tipo de descoordinación con la planta; todo debió ser muy preciso y coordinado.
Ambos megaproyectos fueron trabajados 100% en base a metodología BIM desde la recepción de la ingeniería por parte de los clientes, hasta el despacho a terreno. Esta metodología fue fundamental para el éxito del trabajo y los principales motivos son los siguientes: Son 2 mega proyectos con una gran cantidad de edificios y piezas involucradas; se detallaron y fabricaron en 2 oficinas diferentes y en ciudades diferentes; y finalmente los proyectos fueron “fast track” con ingeniería de diseño que al momento de ser entregada al Consorcio se encontraba con varios temas pendientes y que se tradujeron en una gran cantidad de cambios de diseño que debieron ser controlados a través de modelos 3D con metodología BIM. En el caso de OGP1, estos cambios significaron detallar el edificio 2 veces.
Más retos
Otro aspecto relevante en estos megaproyectos fue ejecutar soldaduras en espesores de acero fuera de lo común, de entre 75 a 100 mm, los cual requirió procesos especiales. “El trabajo con espesores de esta magnitud es completamente distinto al de una estructura común cuyos espesores habitualmente no exceden los 20 mm; se deben elaborar procedimientos específicos para procesar estos aceros, las soldaduras deben ser realizadas personal calificado especialmente para estos espesores, controlándose la temperatura del acero, material de aporte, y muchas otras variables que deben ser estrictamente vigiladas para asegurar la calidad del producto final”, apunta Mario André.
Otro reto técnico fue el montaje de estructuras de gran tamaño.Destacan las columnas que hacen de soporte de los molinos y chancadores; cada columna pesaba más de 100 toneladas; que equivale aproximadamente al peso de 3 galpones industriales de 50×25 metros. Para poder montar este tipo de elementos se requieren grúas con capacidades de más de 1200 toneladas.
En Sierra Gorda, el alcance del trabajo fue el cálculo de las conexiones, modelamiento 3D, detallamiento, fabricación y aplicación del sistema de pintura para las 30.000TM aproximadamente de estructuras que componen todos los edificios principales del proyecto, tales como: Harneros, Chancadores, Molienda, Remolienda, Flotación, Filtrado, Espesadores, Planta de reactivos, Planta de aire, entre otras áreas.
Prearmado en OGP1
Además de la fabricación de estructuras de gran envergadura, para el proyecto OGP1, el cliente solicitó el prearmado en la planta de las columnas principales del edificio de molienda. “Para el caso de las columnas del edificio, cuyos pesos superaban las 100 toneladas y espesores de acero sobre 100mm, el cliente nos solicitó realizar el prearmado a efectos de poder verificar el calce en taller; lo que sucede es que este tipo de elementos son tan grandes y pesados, que no se pueden procesar por las máquinas de corte y perforado automático CNC que se utiliza habitualmente en plantas de fabricación de estructuras”, comenta André. Cuando se fabrican estas columnas, alas y almas se dimensionan y perforan por separado, luego se arma el perfil, y posteriormente se mecanizan las superficies de contacto entre columnas; entonces, “para verificar el alineamiento de las baterías de pernos es necesario realizar un estricto control dimensional, que incluye el prearmado de las columnas que pueden provocar problemas de calce si no se toman los resguardos necesarios”, prosigue el ejecutivo de Arrigoni Metalúrigica. Además, por restricciones al peso máximo admisible en carretera, se debieron seccionar las columnas en tramos más pequeños, cada uno de 30 toneladas aproximadamente, los cuales posteriormente fueron ensamblados en taller para la verificación dimensional.
Ficha Técnica
Proyecto OGP1
Cliente: BHP Billiton.
Ubicación: II Región de Antofagasta.
Ingeniería: Bechtel.
Fabricante: Arrigoni Metalúrgica S.A.
Constructor: BSK.
Proyecto Sierra Gorda
Cliente: Compañía Minera Sierra Gorda.
Ubicación: II Región de Antofagasta.
Ingeniería: Fluor.
Fabricante: Arrigoni Metalúrgica S.A.
Constructor: Salfa Montajes.