Fabricar elementos de hormigón que tengas una geometría no convencional -que sean, por ejemplo, curvos u ondulados- requiere, en la actualidad, de moldajes especiales, lo que hace que el proceso constructivo sea poco eficiente. Con la aplicación de robótica y diseño 3D, una malla electrosoldada, que actúa como refuerzo y molde a la vez, podría cambiar este paradigma y llevarlo a un camino mucho más eficiente y productivo.
Fuente: Hormigón al Día
Uno de los desafíos que tiene la construcción con hormigón es la fabricación de elementos con geometrías no convencionales, de manera tal que todo lo que se involucre en el proceso constructivo funcione de manera optimizada y eficiente, evitando, por ejemplo, pérdida de material o controlando -o reduciendo- la generación de residuo en obra durante la construcción de dicho elemento.
Los elementos de geometrías curvas o no convencionales, para los métodos de construcción tradicionales, transitan por la vereda opuesta. Esto, porque para su fabricación se requieren de encofrados especiales, diseñados sólo para una obra específica y los que muchas veces se utilizan una única vez: en la obra donde se produzca la estructura curva. Esto genera que, si bien es posible fabricar este tipo de elementos, bajo los métodos actuales sea poco óptimo y hasta prohibitivo.
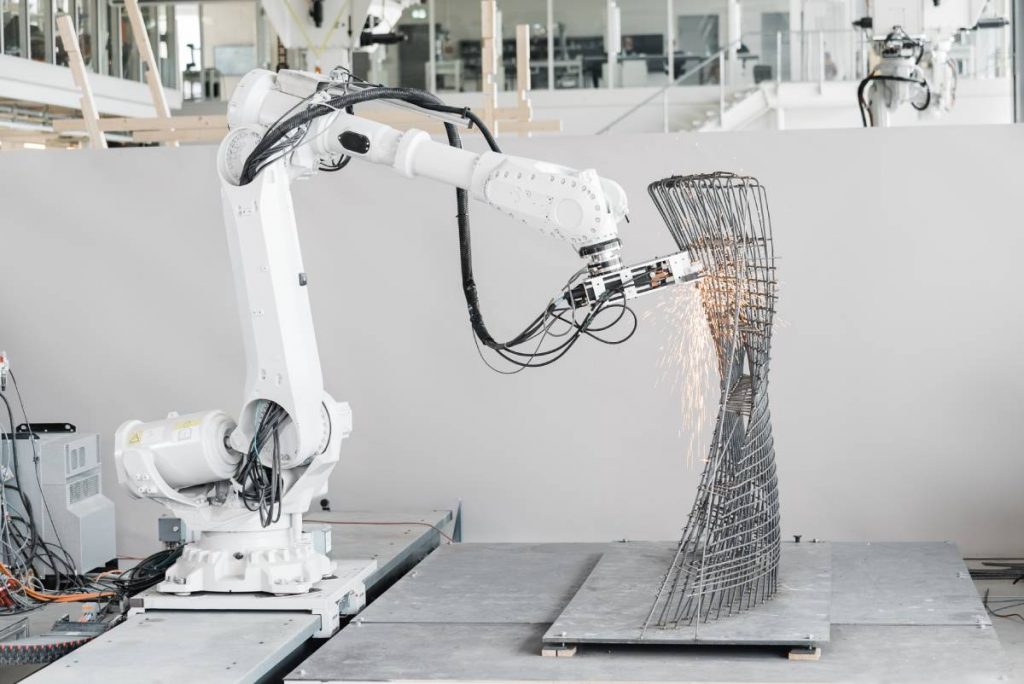
Entre los años 2012 a 2014, la Escuela Politécnica Federal de Zúrich -ETH Zúrich- a través del Centro de Investigaciones Gramazio Kohler, desarrolló un interesante proyecto destinado a optimizar la fabricación de elementos estructurales con geometrías no convencionales: el “moldaje de malla”, una nueva forma de incorporar refuerzo y forma para producir elementos de geometrías no convencionales, sin la necesidad de tener moldajes especiales.
Este proyecto, cuyo funcionamiento in situ se apreció en la casa-laboratorio del ETH Zúrich, la DFAB House, contó con dos etapas y recientemente, recibió el espaldarazo de dos grandes del mundo de la construcción (PERI y Sika) para pasar a una fase industrial de desarrollo.
Los primeros pasos del “moldaje de malla”
El “moldaje de Malla” consiste en la fabricación, vía robot, de una malla que sirva tanto como malla de refuerzo y molde para construir elementos que sean estructurales -muros o losas, por ejemplo- y que tengan geometrías no convencionales. Para ello, además de la robótica, también se utilizó el diseño digital 3D para la conformación de esta nueva “malla estructural”, la que actúa tanto como encofrado como refuerzo del hormigón.
En la primera etapa, que se llevó a cabo entre 2012 y 2014, el “moldaje de malla” consistió en una malla de polímero, fabricada por un robot industrial que extruía el material y, en acuerdo con el software de diseño digital 3D, se generaba la malla. Una vez con este molde fabricado, se realizaron pruebas para verificar su resistencia ante la densidad del hormigón, especialmente cuando el material se vertió sobre este elemento.
En esa primera fase de la malla, lo que se hizo fue suplir la poca capacidad de carga de la extrusión vía robot con la alta capacidad para conseguir una coordinación espacial. En ese sentido, “un uso óptimo de la máquina requiere un proceso constructivo con una transferencia de masa mínima y un alto grado de definición geométrica”, explicaron desde el Centro de Investigación Gramazio Kohler.
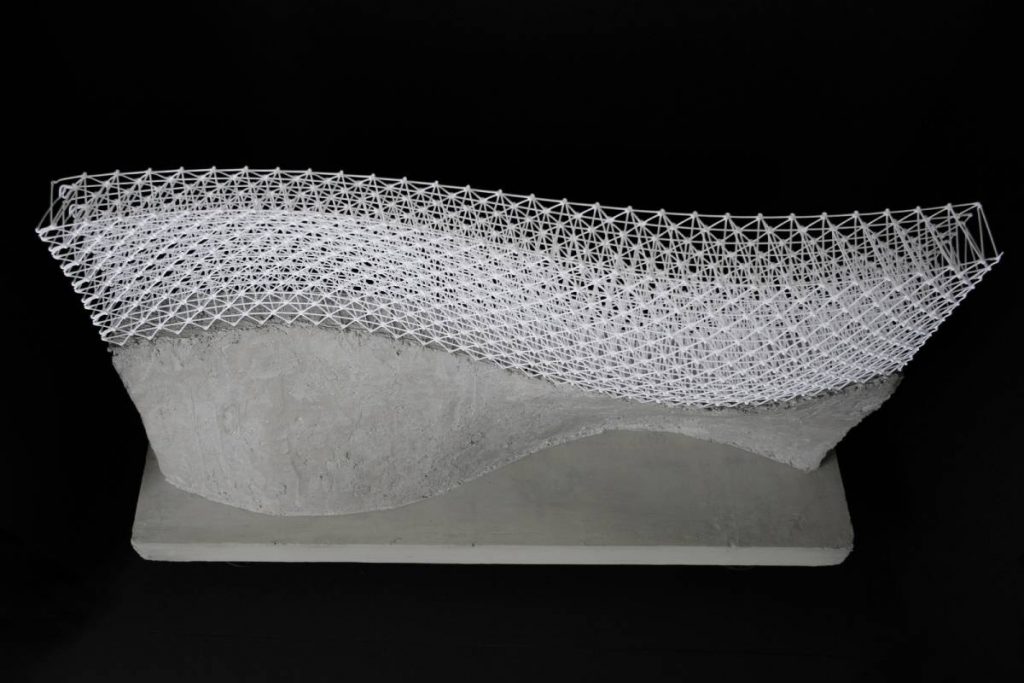
Una vez realizados los ensayos con la malla de polímero, se pasó a una segunda fase: la fabricación de una malla electrosoldada de acero.
La transición de polímero a elemento estructural de acero
En el caso del “moldaje de malla” en acero, la extrusión fue el primer cambio que tuvo el proyecto. “Para ello -comentaron desde el centro de investigación- la investigación se centró en la automatización completa del proceso de doblado y soldado de mallas fabricadas con alambres de acero de 3mm de espesor”.
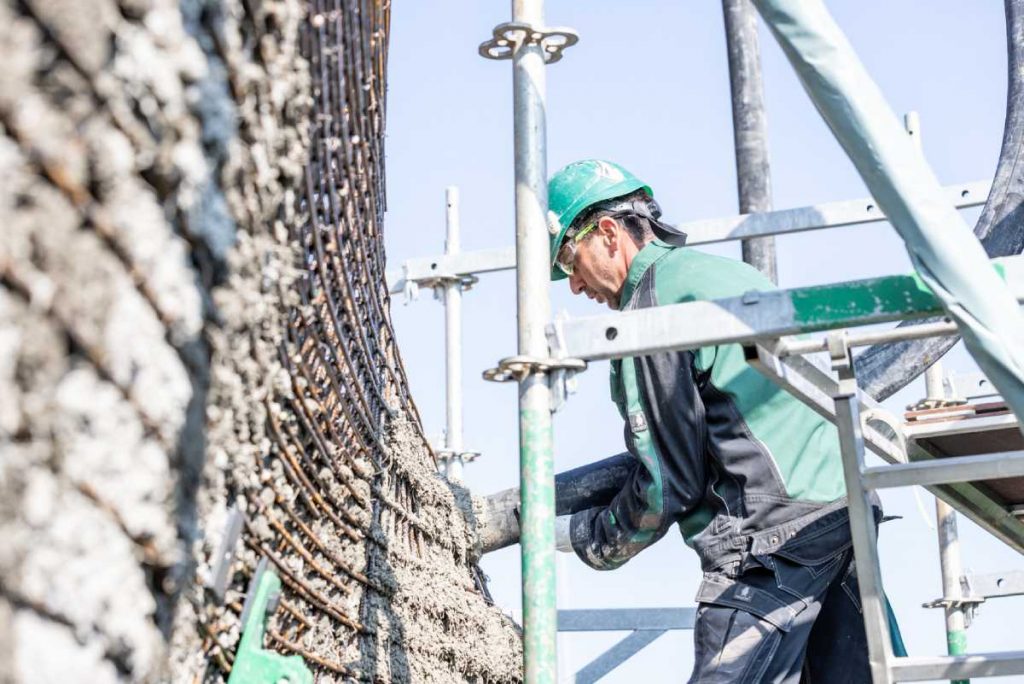
Con esto, se apeló a la resistencia y maleabilidad del metal, junto con la densidad de la malla, para controlar así al hormigón vertido y remover al encofrado de la ecuación. Luego de los primeros ensayos, los alambres de la malla electrosoldada cambiaron su grosor a 6mm.
La segunda fase tuvo su punto cúlmine en 2018, cuando se utilizó esta nueva tecnología para la construcción de un muro curvo y ondulado en la casa-laboratorio DFAB House, del ETH Zúrich. El elemento, de 12 metros de largo, es el muro de carga principal de toda la edificación y de acuerdo al proyecto, soporta una carga de aproximadamente 100 toneladas, las que vienen desde un cielo de hormigón y dos unidades de material ligero, ubicadas sobre el cielo.
El futuro de una nueva tecnología constructiva
Los datos de DFAB House llevaron a que gente como PERI y Sika apostasen por sumarse al desarrollo industrial de esta tecnología. “Estamos apostando y colaborando en el desarrollo de esta joven tecnología desde sus primeros desarrollos”, comentó Thomas Imbacher, Managing Director en PERI SE y responsable del área de Innovación & Marketing. “Creemos en el potencial que tendrá esta nueva metodología constructiva en varios campos de la construcción con hormigón y estamos ansiosos de desarrollar esta tecnología a largo plazo, en conjunto con los otros actores”.
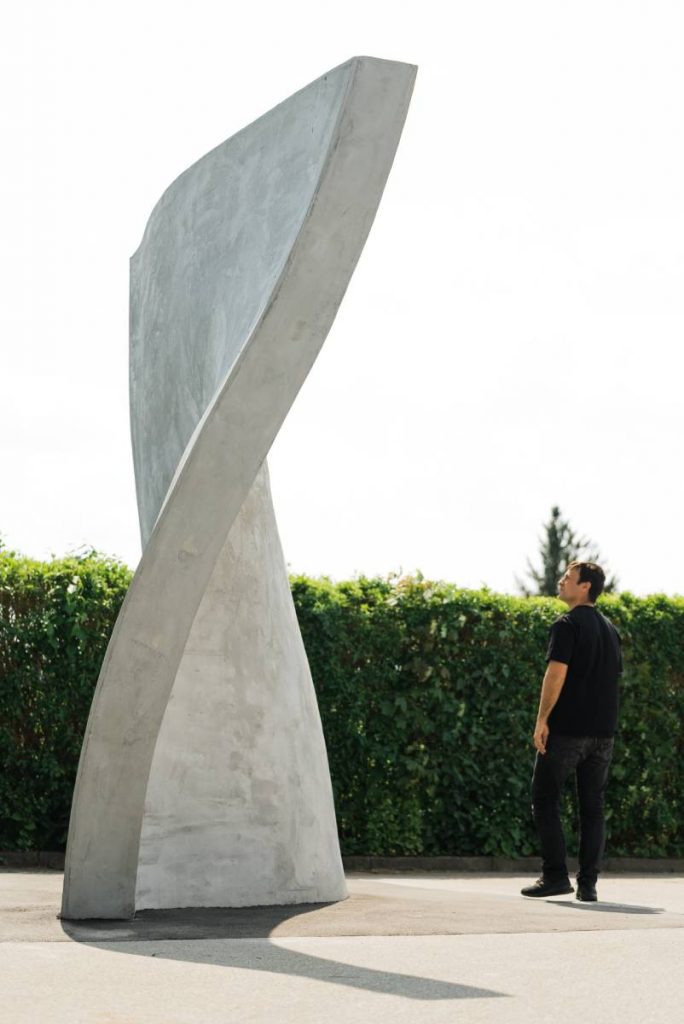
Por su parte, Philippe Jost, líder del área de construcción en Sika, agregó la relevancia de incrementar la presencia de tecnologías de automatización y digitalización en el sector, las que “permiten aumentar la productividad, al tiempo que abren la puerta para nuevos diseños y posibilidades para los arquitectos. A través de este trabajo colaborativo, es posible establecer un nuevo tipo de construcción que permita la producción de geometrías complejas de manera más eficiente que con la metodología tradicional”.
Si bien aún no se conoce en qué proyecto podría utilizarle este “moldaje de malla”, lo cierto es que, con esta tecnología, la construcción con hormigón dará un salto efectivo en la fabricación de elementos estructurales de formas complejas, de manera eficiente y sostenible.