El nuevo reactor piloto de la ‘start-up’ Boston Metal es otro paso hacia la ampliación de su tecnología de acero libre de emisiones
Fuente: MIT Technology Review
Subiendo las escaleras para ver el proyecto más reciente de Boston Metal, queda claro cómo de grande es el trabajo que hay que hacer para reducir el impacto climático del acero.
Esta impresionante y nueva instalación es un reactor piloto que esta start-up utilizará para fabricar acero libre de emisiones. Tiene aproximadamente el tamaño de un autobús escolar y unas escaleras, con barandillas amarillas recién pintadas, llevan a la parte superior. Aun así, en la industria del acero, que produce casi 2.000 millones de toneladas al año, la posible producción de esta instalación es una gota en el océano.
La fabricación de acero industrial genera alrededor de dos toneladas de emisiones de CO2 por cada tonelada de acero producido, lo que supone casi el 10% de las emisiones de CO2 en todo el mundo. Se espera que el mercado mundial del acero crezca alrededor de un 30% para 2050, fecha en la que algunas de las mayores siderúrgicas se han comprometido a alcanzar cero emisiones netas. A menos que se produzcan grandes cambios en la industria, y rápido, este objetivo podría estar fuera de su alcance.
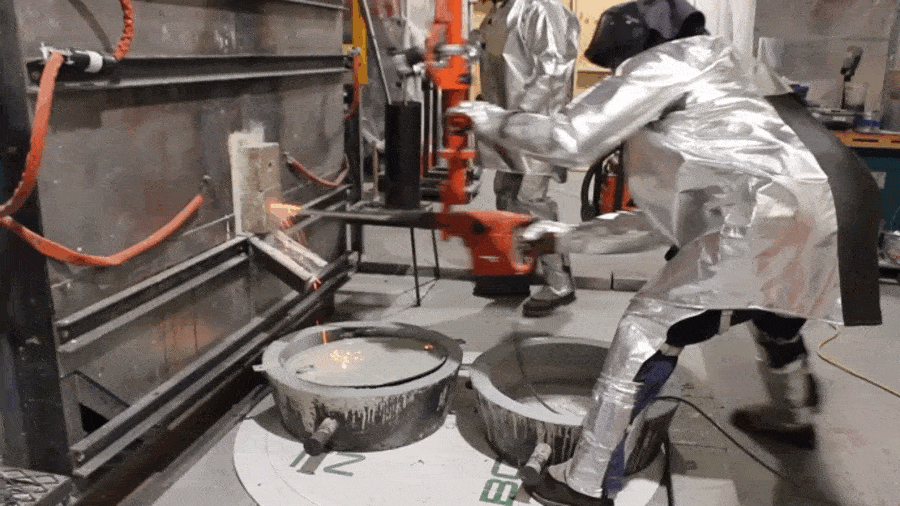
El nuevo reactor de Boston Metal, instalado recientemente en su sede al norte de Boston, es un paso importante en el viaje de la empresa hacia la comercialización. Desde su fundación en 2013, esta start-up ha desarrollado un proceso para fabricar acero verde, resolviendo los detalles en ejemplos más pequeños. El nuevo reactor, junto con una próxima ronda de recaudación de fondos, representa el próximo salto para la empresa en su intento de escalar.
Si Boston Metal realmente consigue escalar su proceso de producción limpia y acceder a suficiente electricidad renovable para ponerlo en marcha, la compañía podría ayudar a resolver uno de los desafíos más complejos a escala mundial a la hora de controlar las emisiones de carbono.
El nuevo enfoque
El acero se usa casi en todo, desde los coches hasta edificios y turbinas eólicas, pero descarbonizar la industria no es nada glamoroso. “La gente no presta mucha atención a los sectores industriales”, afirma el CEO de Boston Metal, Tadeu Carneiro. “Es una industria muy conservadora y es difícil suprimirla”.
Los combustibles fósiles son esenciales para la actual producción de acero. La mayor parte de la fabricación de acero empieza en un alto horno, donde el material derivado del carbón llamado coque, que es casi carbono puro, reacciona con el mineral de hierro (una mezcla de óxidos de hierro y otros minerales). Esa reacción extrae el oxígeno, dejando hierro líquido. Luego, el carbono y el oxígeno se liberan juntos como CO2.
La solución de Boston Metal es un enfoque completamente nuevo, llamado electrólisis de óxido fundido (MOE, por las siglas en inglés de molten oxide electrolysis). En vez de usar el carbono para eliminar el oxígeno, el proceso se basa en la electricidad, que pasa por una célula llena de una mezcla de óxidos de hierro disuelto junto con otros óxidos y materiales. La electricidad calienta la célula hasta aproximadamente 1.600 °C, derritiéndolo todo en una caliente sopa de óxido.
Además de calentarlo todo, la electricidad impulsa las reacciones químicas que eliminan el oxígeno. El hierro fundido se acumula en el fondo del reactor y se emite oxígeno en lugar de CO2.
Debido a que las impurezas quedan en gran medida fuera de la reacción, el proceso MOE puede funcionar con mineral de hierro de baja calidad, lo que podría ser un importante beneficio añadido de esta tecnología, según afirma Carneiro.
Crecer
El proceso de fabricación de acero de Boston Metal fue desarrollado por los investigadores de materiales del MIT, Donald Sadoway y Antoine Allanore, a mediados de los 2000. La investigación progresó en pequeños reactores del tamaño de una taza de café. Estas versiones de laboratorio producen una cantidad de hierro del tamaño de un cacahuete en un par de días.
Un gran desafío hasta ahora en la transición a reactores más grandes tiene que ver “con la estabilidad del ánodo inerte”, una pieza de metal hecha de una mezcla de acero y cromo, según explica Stephan Broek, vicepresidente de tecnología de Boston Metal. Si el reactor funciona como debería, el ánodo no participa en la reacción: solo proporciona una forma de que la electricidad se mueva a través de la célula. Pero el ánodo tiende a degradarse rápidamente si el equilibrio entre las condiciones como la distribución de corriente y la química del electrolito no es del todo correcto.
Este y otros desafíos son los que afronta el nuevo reactor piloto, que es unas mil veces más grande que la versión de laboratorio.
El nuevo reactor funcionará con una corriente de hasta 25.000 amperios (un hogar típico usa entre 100 y 200). Está equipado con varios ánodos y con todos los elementos con los que debería contar la futura célula de tamaño industrial, que sería todavía más grande (unas 10 veces mayor).
La construcción del reactor piloto está casi terminada y las pruebas están programadas para agosto. Primero, se usará con ánodos de carbono para producir ferroaleaciones, metales de alto valor que se pueden crear en un proceso de electrólisis similar al que se usa para fabricar acero. Después de probar el reactor para ese producto, el equipo planea transformarlo para producir acero a principios del próximo año, según explica Broek.
El bebé de la industria
La puesta en marcha del reactor piloto representa uno de las mayores metas volantes de Boston Metal antes de construir un proyecto de demostración de tamaño comercial, que estará compuesto por cinco células más grandes unidas y que se espera que estar terminado en 2026. La start-up está en el proceso de recaudar el dinero para llevarlo a cabo.
Con una instalación comercial puesta en marcha, la empresa planea patentar su tecnología y trabajar con las siderúrgicas existentes para instalar y operar los reactores.
Pero un proceso como MOE, que es novedoso para la industria, tardará tiempo para integrarse con los actores existentes. “Todavía necesita un par de años de prueba y demostración para comprobar si realmente se puede escalar. Y aún no sabemos realmente cuánto costaría”, opina Max Åhman, profesor de sistemas ambientales y de energía de la Universidad de Lund (Suecia).
Otros nuevos enfoques -ya en fase de prueba- pueden ser más sencillos de demostrar y escalar, añade Åhman. En concreto, el proceso llamado reducción directa, que se utiliza ampliamente en la actualidad, se puede modificar para producir acero libre de emisiones.
La reducción directa generalmente usa el gas natural para reaccionar con el mineral de hierro sólido. Este proceso, como la fundición en un alto horno, también libera CO2, porque es el carbono del gas, que es principalmente metano, el que reacciona con el oxígeno del mineral para separarlo del hierro. Pero si se usa hidrógeno en vez de gas natural, se emite vapor de agua.
La siderúrgica sueca SSAB está construyendo una gran instalación piloto para probar la reducción directa impulsada por hidrógeno que está programada para alcanzar la producción a escala industrial alrededor de 2026.
Carneiro reconoce que las siderúrgicas que usan hidrógeno podrían tener una ventaja, aunque argumenta que MOE con el tiempo será atractivo para algunos fabricantes de acero, ya que puede usar una variedad más amplia de materia prima y no solo el mineral de alta calidad requerido para la reducción directa.
No obstante, ya sea que los productores de acero recurran al hidrógeno o a un proceso impulsado por electricidad como el MOE de Boston Metal, necesitarán mucha más electricidad renovable para reducir las emisiones.
Una estimación de los investigadores de la Universidad de Columbia (EE UU) encontró que si la producción mundial de acero en los altos hornos se convirtiera al proceso MOE de Boston Metal, se necesitarían más de 5.000 teravatios-hora de electricidad para hacerlo funcionar, aproximadamente el 20% del consumo mundial de energía en 2018. Producir el acero con hidrógeno también tendría elevados requisitos de electricidad.
Si esa electricidad proviene de combustibles fósiles, cambiar la producción de acero por la electricidad sería pasar de una fuente de emisiones a otra. Pero si proviene de energías renovables u otras fuentes libres de carbono, eso podría hacer una mella importante en la contaminación por carbono.
Los investigadores también encontraron que los precios de la electricidad tendrían que bajar significativamente para que el proceso sea económico.
A pesar de las promesas de las nuevas tecnologías, todavía queda un largo camino por recorrer antes de que realmente se consiga reducir las emisiones. “Hay mucho blanqueo verde en la industria del acero, además de que la gente es optimista sobre el progreso en una etapa muy temprana”, señala Rebecca Dell, responsable de industria en la organización sin ánimo de lucro ClimateWorks,
“Es fácil, si no se presta atención, confundir el entusiasmo por los proyectos en etapa inicial con el verdadero progreso”, agrega.
Puede que a Boston Metal le queden muchos pasos para producir acero verde a una escala significativa, pero Carneiro, al menos, está ilusionado de seguir ese camino. Su gran energía se nota mientras describe los planes de la compañía y habla sobre el futuro. “No creo que haya otra oportunidad en el mundo tan grande como esta. Es realmente enorme”, asegura, al recordar que se necesita acero para todo.
Con todos los ojos puestos en esta industria que es uno de los mayores contaminantes de carbono del planeta, “el sentido de urgencia está aquí ahora”, concluye el CEO.