Fuente: 3D Natives
El resultado es una drástica reducción de peso ya que se ha reducido un 80% del peso que las soluciones actuales, facilitando considerablemente su transporte y la energía necesaria para montarlas. De hecho, los diversos componentes impresos en 3D que forman la viga encajan tan fácilmente como los ladrillos de LEGO.
Muy utilizado por la industria de la construcción, el hormigón armado está, como su nombre indica, compuesto de hormigón y metal, con mayor frecuencia acero. Se trata de un material compuesto que puede soportar tracción y compresión, además de altas cargas. Sin embargo, es un material que sigue siendo muy pesado de transportar, y la presencia de acero aumenta considerablemente el peso de la viga. Por lo tanto, los investigadores intentaron reducir esta limitación tanto como fuera posible y trabajaron durante 3 años en un proyecto de impresión 3D. José Ramón Albiol, profesor de la Escuela Técnica Superior de Ingeniería de la Edificación (ETSIE) en la UPV, añade: “Nuestro objetivo era dar una alternativa a las actuales estructuras de hormigón armado. Estos consisten en perfiles construidos en toda la longitud de la pieza, lo que requiere instalaciones costosas y es difícil de transportar”.
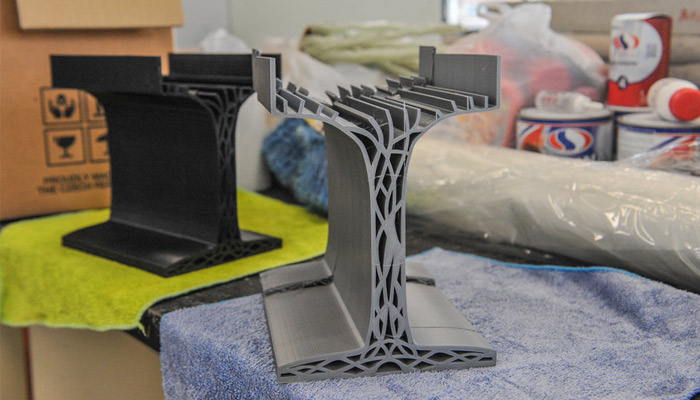
Los investigadores del proyecto no han dado muchos detalles sobre el proceso de impresión 3D utilizado. Solo sabemos que favorecieron la utilización de plástico reciclado para reducir la huella ecológica, y que se inspiraron en la forma de los huesos humanos para diseñar los modelos 3D. El objetivo del proyecto era reproducir la estructura de la epífisis, la parte terminal de los huesos, formada por varias capas que le confieren una rigidez significativa a la vez que se mantiene ligera. Gracias a la fabricación aditiva, los investigadores pudieron imitar esta estructura de panal y colocar el material donde se necesita.
El resultado lo encontramos en una reducción del peso total gracias al uso de plástico en lugar de acero, así como una mejor distribución del material. José Ramón Albiol añade: “Se trata de una estructura de panal, que reduce el material plástico utilizado, y por tanto su peso, manteniendo la rigidez estructural. Y eso es lo que transferimos a estos rayos revolucionarios. Es un sistema natural muy inteligente y su reproducción en estas vigas les confiere, con un bajo peso estructural, una altísima capacidad mecánica”.
Concretamente, los investigadores imprimieron en 3D bloques capaces de encajarse los unos con los otros, como los ladrillos de LEGO. Luego se agrega una capa de hormigón para formar la viga final. Más allá del peso reducido, este método permite obtener una estructura modular acorde a las necesidades y al proyecto de construcción. De esta forma, los bloques son más fácilmente transportables, con una instalación que se realiza in situ, simplificando así la mano de obra necesaria.Miguel Sánchez, del Departamento de Sistemas e Informática (DISCA) en la UPV, concluye: “La impresión 3D permite fabricar piezas a medida muy cerca de la zona de ejecución, lo que también simplifica el transporte, reduce los costes y facilita la personalización. La posibilidad de personalizar las vigas in situ permite adaptar las características de cada una de ellas a las necesidades estructurales de cada punto de construcción. La capacidad de reciclar los materiales poliméricos para producir las vigas reduce significativamente su huella de carbono”.
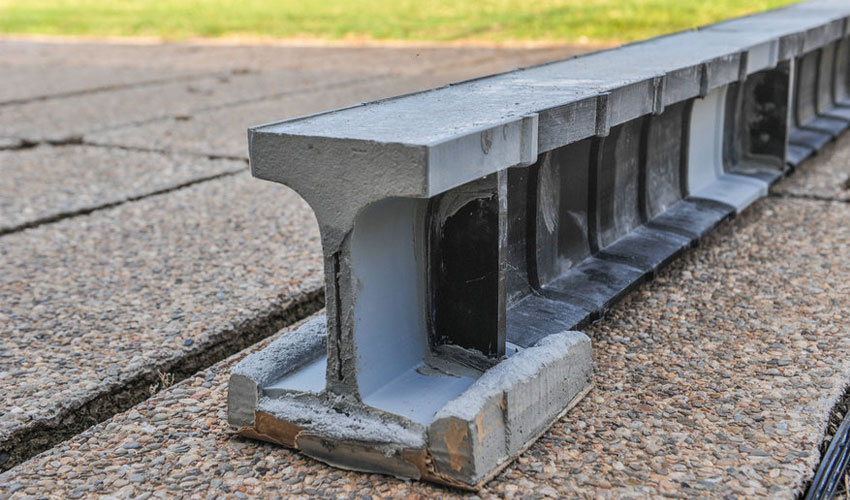